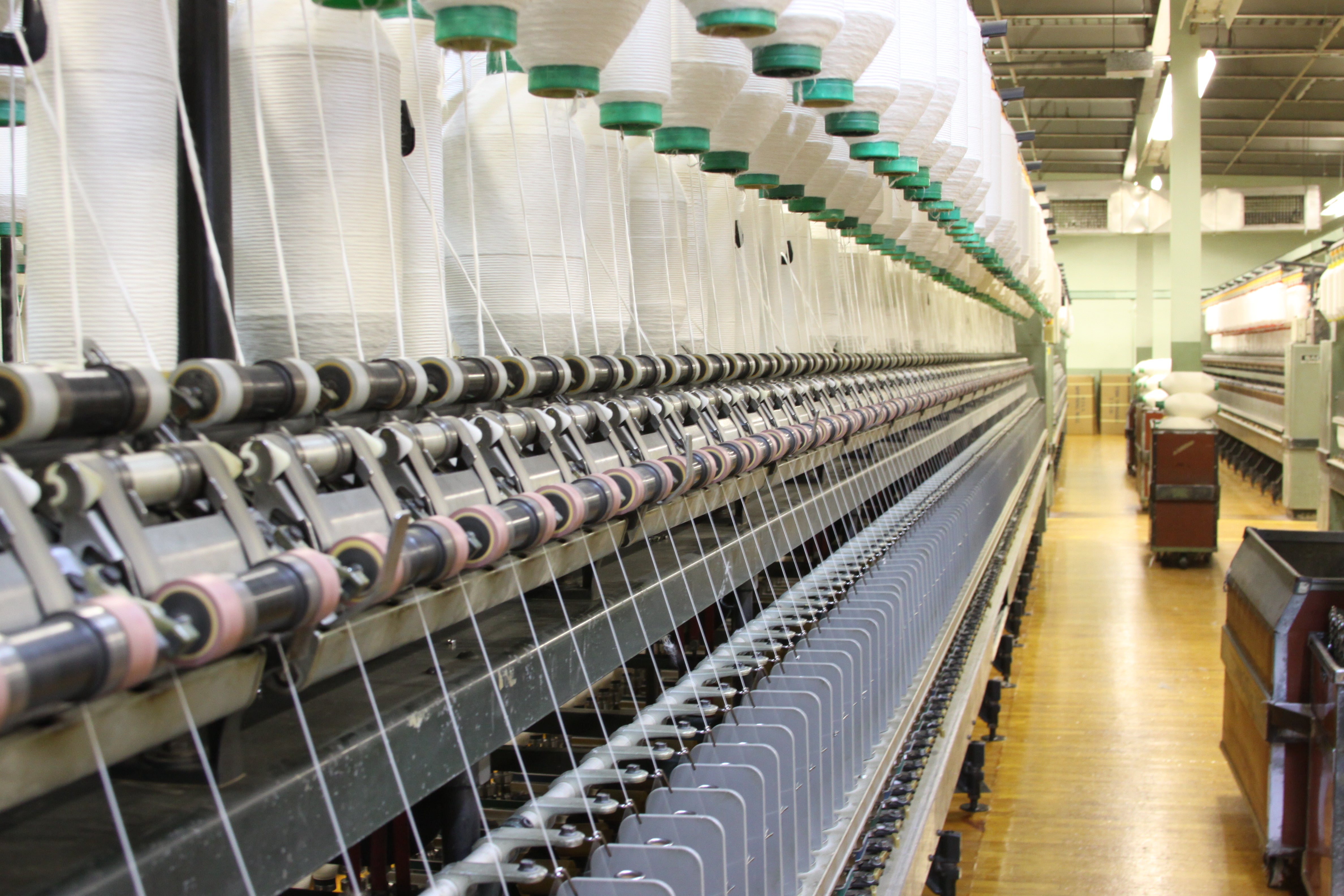
Inside the American Spinning Factory That Makes Our Top-Quality Cotton Yarns

The softness and durability of Solid State Clothing t-shirts are directly connected to the quality of the cotton they're made from. Before our comfortable tees ever make it into your closet, the cotton that goes into them has been on quite a journey — from the field to the cotton gin to the spinners, knitters, sewers, and dyers.
Today we take a deep dive into one part of that journey — the cotton spinning process — to get a better understanding of what makes our cotton t-shirts the best of the best.
To get the inside scoop, we chatted with Andy Long, VP of Sales and Marketing at Parkdale Mills Spun Lab Division. Parkdale Mills is based in Gastonia, NC and stands out in the manufacturing world as a leading manufacturer of spun yarns. One thing we especially appreciate about the company leadership is their commitment to zero-waste manufacturing. They do a phenomenal job of reducing waste, recycling, and reusing materials whenever possible.
But let’s talk about the spinning process and the quality of cotton they produce that contributes to the quality of our t-shirts.
Cotton Spinning Starts with Choosing the Cotton
The spinning process starts with choosing the best cotton bales based on the quality of the cotton. “We go through the US Department of Agriculture (USDA),” Long says. “The USDA has a controlled process, and they classify each bale of cotton they've collected and ginned. They take a chunk out of each one and run it through a machine that provides all the data about the character of the cotton — the length, the diameter, the color, the amount of trash, the whole gamut of specs that we look at to determine the quality of the cotton. We take the USDA’s data and engineer what we call our laydown…”

The laydown at Parkdale is a group of about 70 bales blended together. And those bales are chosen specifically for their similarities. Long says, “There’s going to be some variation in the size of the cotton, the length of it, its diameter, the amount of 'trash' in it, the yellowness or the whiteness of the cotton. You could get one field that didn't get a lot of rain that year, so that cotton’s a little thinner than the cotton from a field that got more robust rain during that season.”
“So we look at the data from all of the cotton bales we have available to us from the merchant, and we pick bales that we can put into a computer system and it will average out those variations and irregularities to make the product as homogenous as possible,” explains Long. “We spend a lot of time, energy, and money on making sure that process is right because the end result can have a big impact on the quality of product that we put out in our cotton.”
The Manufacturing Process Begins
After the laydown is engineered, the manufacturing process can begin. “A machine goes across the tops of the bales and down the linear line,” Long says. “It takes an inch and a half, two, or three inches of cotton off the top of each bale so that you continuously get the average of variations you’re working with. And that starts the manufacturing process.”
Cleaning the Cotton
Then the cotton goes into a cleaning process. “We use air and force the cotton into different types of machines with screens and beater bars that move and agitate it so that as much of the vegetable matter that's in the cotton will fall out,” explains Long.
Carding
Following the cleaning process, forced air transports the cotton to the carding process via large ducts mounted on the ceiling above the manufacturing equipment.
“Carding is really the workhorse of a cotton mill,” Long says. “You can imagine the cotton that comes out of the field and goes through the cleaning process. It's tangled. It's mangled. There's no uniformity to it at all. The carding process starts to align the fibers. It also takes trash and some short fibers out.”
The cotton comes out of the carding process in a web and goes into sliver form. Sliver is simply the name for the long strands of cotton fiber. The carding sliver — the cluster of strands that result from the carding process — goes into a can, and the can moves along to the next process: drawing.
Drawing
“Drawing is a process in ring spinning that helps ensure uniformity,” says Long. “We’re trying not to have one section of the product that has more porous fiber or spider fiber, longer fiber or shorter, yellow fiber versus white.”
“To do that, we’re taking multiple cans of sliver (usually eight) from the card and combining them into one sliver, so we’re getting additional blendings/doublings,” Long explains. “We then take multiple (usually six) cans of sliver from the first drawing process and make one end from these six in a second drawing process — again, giving us more blending/doubling to ensure we're increasing uniformity. In ring spinning, we normally go through at least two processes, sometimes three processes of drawing.”

Combing Ringspun Cotton
After drawing, the cotton either goes through a combing process or goes directly to roving. “Combing is the most expensive ring spinning process we do, and it's more expensive because we’re taking out more weight than ever,” says Long. “The combing process will take out approximately 25% of the total volume of the product in short fiber. And that’s creating a more luxurious yarn, a longer staple length, a higher sheen. Combed cotton simply has better all around characteristics.”
It's worth noting that we make Solid State t-shirts from ringspun cotton, the cotton that's gone through these additional processes so that it's more luxurious, softer, and a better quality overall.
Roving
Both combed and carded cotton go next to roving. “Roving really doesn't do a lot to the product itself,” Long explains. “As far as improving it, roving takes it from the form of sliver into a smaller form — a sliver is about the size of a broomstick, and roving is about the size of a pencil.”
“The fiber’s got very little twist to it at this point,” Long says. “The fibers are all parallel and being held together by fiber-to-fiber cohesion. With very little twist, they just pull apart like a cotton ball. So when the product goes to roving, the fibers go through a two-roll process. The back row’s turning a little slower than the front roll, so it’s adding twist and starting to elongate and make a narrower substrate."
“The little bit of twist will help hold the fibers together during processing,” adds Long. “As the roving bobbin moves into the spinning frame, the roving itself comes down through the spinning frame and goes through processing. It’s pulled in the process, so it has to have enough cohesion and twist that it’ll allow the process.”
Spinning Cotton

A lot has happened in preparing the cotton for spinning. At this point, it’s ready. “Roving goes in the top of the spinning frame, and it’s processed downward,” explains Long. “It goes through the spinning process which again is a two-row process where the back row is turning slower than the front row. And it’s elongating the fibers, drawing them apart and adding twist so the product will stay together.”
How much twist the process adds depends on the size of the yarn and the application it’ll be used for. “If it's going into weaving, we add more twist to give it more strength.” Long says. “Knitting takes a little less twist. If a manufacturer is making hosiery sock knitting, it takes even less twist.”
Winding It
Following spinning, the product moves on to winding, a process that’s automated at Parkdale. “The spinning frame is doffed automatically, and the spinning bobbins are fed to a winder,” Long adds. “The process takes 15 to 20 bobbins of yarn and makes them onto one comb that's more manageable for a knitter or weaver for their process.”
Conditioning the Cotton
“From winding, cotton goes through a conditioner to add a little bit of moisture back into the yarn after processing,” says Long. “That helps with shedding and gives it a little more tenacity or elongation.”
Finishing - Packing and Strapping
After finishing the conditioning, it’s time to pack and strap the cotton — either in a cardboard case or on a plastic reusable pallet. From there, it’s out the door to manufacturers like us.
Want to know more about our 100% cotton made-in-USA t-shirts? Visit our shop to buy the softest, longest lasting t-shirt you'll ever wear.